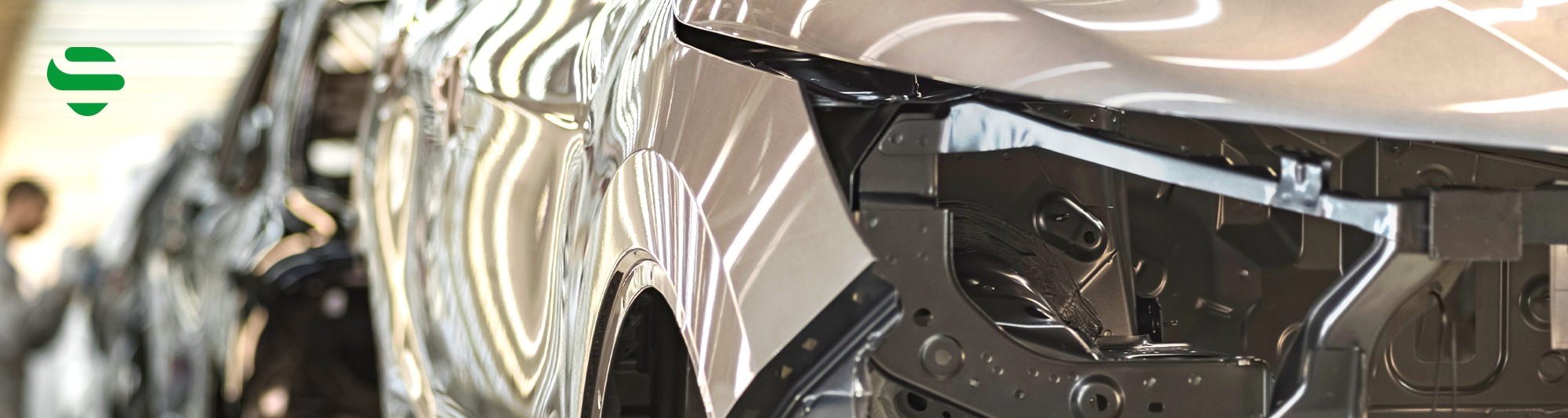
Six Ways Geolocation Technology Enhances Car Manufacturing
By Lubomir Mraz | April 24th, 2024 | 10 min read
Car manufacturers face constant pressure to enhance production efficiency. With the average car having a production lifespan of 6 to 8 years, there’s a clear need to reduce manufacturing costs by streamlining operations on the shop floor. To remain profitable, production needs to be as much as 40% cheaper in the last year of production compared to the first.
Naturally, this relentless push for greater efficiency is a major driver of innovation, not only in manufacturing plants themselves but also across the entire supply chain. Car manufacturers, known for their demanding standards and cutting-edge production techniques, have pioneered lean manufacturing processes to reduce waste and improve efficiency. Nonetheless, the rising demand has stretched even these methods to their limits.
To shift gears and make room for future growth, car manufacturers must constantly transform. This means adopting new and emerging technologies, such as indoor and outdoor geolocation systems. By gathering real-time geolocation data from assets such as material handling units and car body parts, manufacturers can improve production efficiency and reaffirm their edge in a highly competitive market.
The strategic use of real-time location data allows car manufacturers to adhere to demanding regulatory standards, pinpoint potential risks or inefficiencies on assembly lines, and enhance offline area management. Data also supports real-time traffic management for intralogistics fleets, significantly improving overall supply chain and factory efficiency. Moreover, analyzing location data over time helps manufacturers optimize facility layouts to maximize the use of space and reduce unnecessary material movement.
In this guide, I’ll share six of the most important use cases for geolocation technology in enhancing car factory efficiency:
Understanding the modern car manufacturing plant
Before I get into explaining the value of these use cases, I’d like to share an example of a typical modern car manufacturing plant – the Volkswagen factory in Bratislava, Slovakia. The plant is the largest of three in the country, and it has been in operation since 1991. The plant produces around 300,000 vehicles and over 20 million components every year. They operate two test tracks and a logistics fleet comprising hundreds of trucks importing components and materials daily. They also employ around 11,000 people.
Check the factory on 🌍 Google Earth !
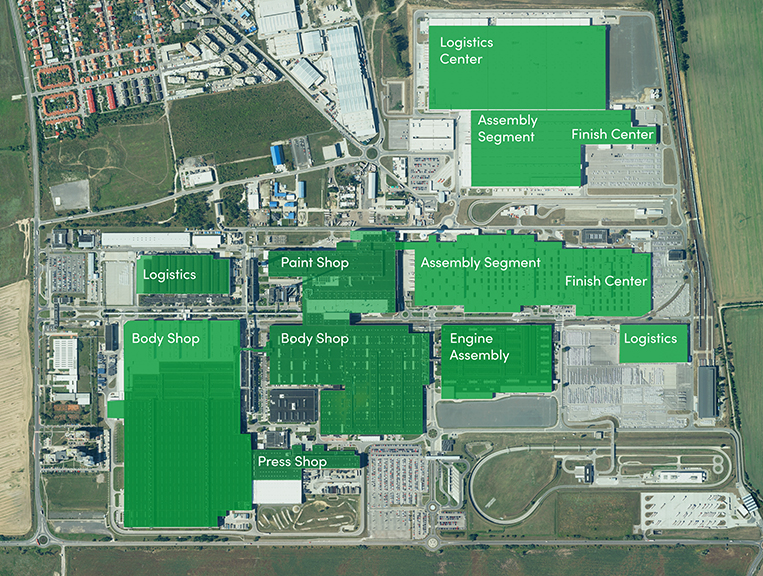
Manufacturing takes place across five main facilities:
- Body shop: Vehicle bodies for SUVs and smaller city vehicles are produced in the body shop. Hundreds of robots handle processes like welding, gluing, soldering, screwing, riveting, joining, and pressing.
- Press shop: Steel and aluminum car facing components are pressed in the press shop. The capacity of the press is around 10,000 strokes per day, with a total power of 91 meganewtons, equivalent to a stack of 4245 SUVs piled in a 7 km-high tower!
- Paint shop: The paint shop is where vehicle bodies get their color using serial painting techniques with several different colors. Each vehicle has four or five layers of paint, which together have an average thickness of a human hair.
- Assembly hall: When the bodies come from the paint shop, they are finished inside and outside in the assembly hall. Parts are brought to the line on a ‘just-in-time’ basis, meaning they arrive at the exact moment they need to be installed in the vehicle.
- Logistics hall: Every day, hundreds of trucks import components that need to be guided to their proper locations. Materials are only imported in their required quantities to avoid overstock and waste, save storage space, and avoid overburdening workers.
With a high-level overview of a modern car plant, let’s explore the specifics of how geolocation technology enhances operations across the end-to-end vehicle manufacturing process. These use cases illustrate not just the application of this technology, but also its transformative impact on production efficiency and overall factory dynamics.
Nutrunners are essential in achieving precise and reliable fastening during the manufacturing process. A typical car assembly line uses nutrunners of many different sizes for fastening parts like wheels, engine components, transmission mounts, or suspension components.
These tools ensure that fasteners are tightened to the specified torque. Accuracy is critical to the safety and reliability of the vehicle. For example, going beyond recommended stress limits can quickly lead to component failure during operations, potentially leading to serious issues for the manufacturer.
The situation is complex for three main reasons:
- A single assembly line typically produces many different car models
- Every individual component requires a different torque
- Many nutrunners are cordless, letting workers move freely around the assembly line
These factors present challenges for error proofing and quality control. It’s difficult to know if the right tool with the right configuration is being used for the right job.
By introducing geolocation-based tracking for nutrunners and car bodies in the assembly hall, operators can increase their efficiency and throughput. In addition, improved quality assurance and reduced risk of human error ensure the car is assembled to meet strict safety and quality standards.
#2. Expedited recovery: Streamlining car retrieval in offline areas
When a car leaves the assembly line, but can’t be shipped due to a quality control problem or a missing part, it’s placed in a special ‘offline’ area indoors or a parking lot. The problem grows due to gaps in supply chains. This leads to more vehicles being put aside until the necessary parts are available to complete them. These include high-tech components equipped with microchips for features like onboard computers or advanced safety systems. With supply chain disruptions now being a recurring challenge in the automotive industry, the problem is likely to grow.
At some point, these vehicles must be located and completed. In these cases, it’s vital to find the right car as soon as possible to minimize downtime. Plants may have hundreds of vehicles stored in offline areas, many of which are the same color. Sometimes, they have dedicated personnel tasked solely with finding the right cars.
To understand the scale of the challenge, let’s consider the VW plant in Bratislava. Below is an aerial photo of one of their outdoor yards, which covers an area of approximately 74,000m2.
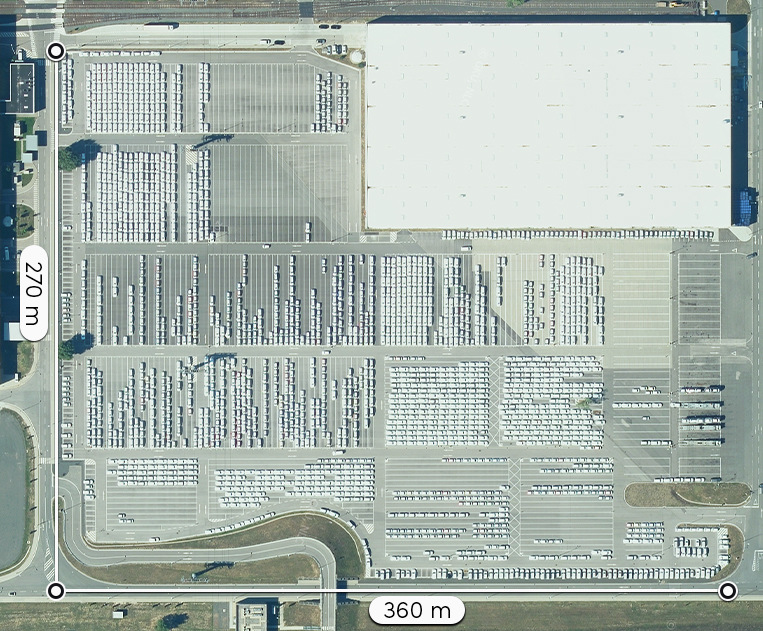
Zoom out on 🌍 Google Earth, and you’ll see there are five more parking lots around the plant.

In this case, the value of geolocation solutions is obvious. By deploying the technology in the outdoor parking yards and assembly halls, manufacturers can greatly reduce searching time and receive automated alerts if there are delays.

#3. Streamlined supply: Advanced tracking for milk runs and tugger trains
In intralogistics, milk runs support lean manufacturing with frequent transport of materials and parts around the plant. This approach draws inspiration from the traditional milk delivery concept, where a milk float drops off fresh milk and collects empty bottles on the same route.
In the context of car manufacturing, milk runs govern the regular, scheduled collection and delivery of materials in a looped route, thereby reducing transport costs and wastage. In this case, the operator will collect materials and supplies from a centralized warehouse and follow a specific route, delivering them across several assembly sites. Large manufacturing plants use tugger trains, which deposit or collect various carts and containers at each station.
Geolocation services provide complete visibility over milk runs and tugger trains to minimize production line downtime. The data collected during operations is also a valuable resource in planning and management. For example, using this data, plant managers can build diagrams and heatmaps to eliminate bottlenecks and minimize cycle times.

Source: www.still.de
#4. Material mastery: Smart tracking for returnable pallets
A great deal of what makes a lean manufacturing process is down to inventory management. Mismanagement or loss of things like returnable pallets, for example, can rack up significant replacement and operational costs. Other challenges include supply chain bottlenecks and an increased risk of understocking or overstocking. Moreover, manual tracking is labor-intensive and prone to errors.
To remedy the problem, many car factories have shifted to paperless manufacturing. Instead of relying on paper kanban boards and other inventory and project management solutions, they’re now using digital solutions like e-kanban. In addition to providing greater control and visibility over operational processes, e-kanban can incorporate geolocation technology to automate many aspects of inventory control and workflow management.
By integrating geolocation services, e-kanban systems can provide continuous tracking and real-time inventory updates. This greatly reduces the risk of misplaced inventory, streamlines the flow of materials, and enhances forecasting accuracy. For example, used inside the press shop, geolocation can track pallets to shorten lead time and enhance production efficiency.


#5. Traffic harmony: Geolocation solutions for complex intralogistics
Transportation inefficiencies are among the major contributors to productivity gaps. Transport waste happens when parts and materials intended for use in production are transferred or handled unnecessarily or in a suboptimal manner. Not only does moving cost time and money; it also increases the chances of materials getting lost, damaged, or misused.
Modern car manufacturing plants rely on a combination of automated and manual vehicles for transportation. However, while autonomous vehicles are critical in lean manufacturing, there are now so many moving parts that the situation has become highly complex. This is further exacerbated by the rising demand for higher throughout and the fact that OEM procurement departments drive down pricing via competitive bids. This results in a fleet of many different vendors that can’t communicate effectively with one another; in other words, operational siloes that hinder efficiency.
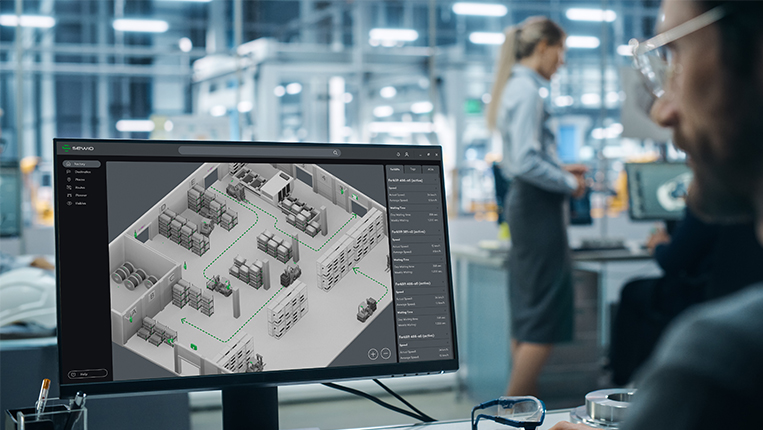
Introducing traffic management with real-time geolocation data from all participants solves this problem, while also helping to mitigate the effects of supply chain disruptions. That way, every AVG, AMR, forklift, and tugger train can operate without interference or misalignment between workers, traffic lights, gates, and tunnels. In other words, you can control the entire traffic flow and get continuous feedback on events in real-time.
#6. Protecting personnel: Advanced geolocation for collision avoidance
As the push for greater efficiency intensifies, intralogistics are becoming more constrained as the number of participants grows. With speed limitations for automated vehicles gradually increasing, the risk of safety incidents is also rising.
To address these concerns, manufacturers are deploying new solutions, such as ultrasound detectors and more complex radio ranging and camera vision systems. However, despite such innovations, these solutions share a common limitation: they lack adequate environmental context. They typically work in isolation, able only to manage safety within a limited visible perimeter around the vehicle or person.
To advance safety, car factories need an orchestrated solution that ‘sees’ beyond things like pallet-racking structures or walls. This allows for the intelligent adjustment of vehicle behavior depending on the proximity and movement of forklifts, whether they’re merely driving close to each other in speed pitlanes or they’re on a collision course. Accurate real-time geolocation of all intralogistics participants is crucial for enabling this higher level of safety management within the factory.

Getting started with geolocation services
The use cases I’ve shared in this guide should help you pinpoint areas that can benefit from precise location tracking in your factory. Start by evaluating your current processes, and implementing these solutions strategically, one stage at a time. By adopting an approach of continuous innovation, you’ll start seeing significant improvements in production accuracy, operational safety, and process efficiency.